|
Steel rolled finish ball screw |
|
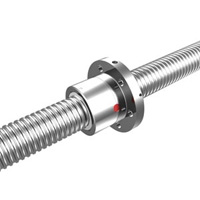 |
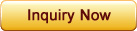
|
A ball screw is a mechanical device for translating rotational motion to linear motion. A threaded shaft provides a spiral raceway for ball bearings which act as a precision screw. As well as being able to apply or withstand high thrust loads they can do so with minimum internal friction. They are made to close tolerances and are therefore suitable for use in situations in which high precision is necessary. The ball assembly acts as the nut while the threaded shaft is the screw.
|
Ball screws are used in aircraft and missiles to move control surfaces, especially for electric fly by wire. They are also used in machine tools, robots and precision assembly equipment. High precision ball screws are used in steppers for semiconductor manufacturing. Small ballscrews are often used to move the read heads of floppy discs and compact disc players.
In contrast to conventional leadscrews, ballscrews tend to be rather bulky, due to the need to have a mechanism to re-circulate the balls. |
The Following is rolled steel finish ball screw production technology information and list. |
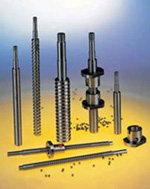 |
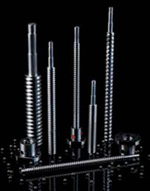 |
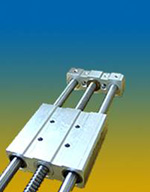 |
Single and double nut ball screw |
Ball Screw Series |
Single and double nut ball screw |
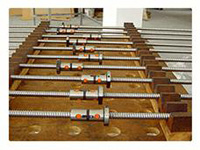 |
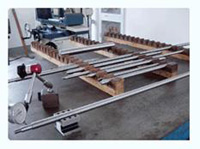 |
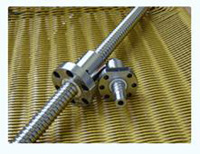 |
Single and Double nut ball screw |
Single and double nut ball screw |
Single and double nut ball screw |
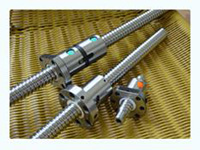 |
|
|
Single and double nut ball screw |
|
|
Inner circulation ball bearing screw: |
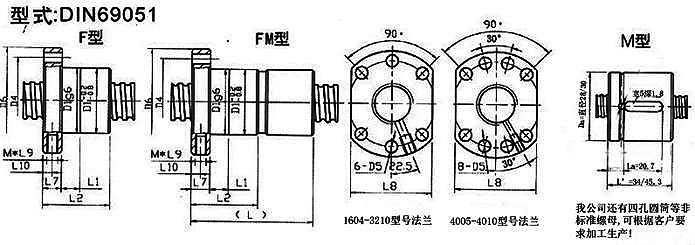 |
Model |
Metric diameter |
Journey |
Stationary hole |
Diameter of steel ball |
Installation and connection dimension of screw cap (mm) |
D1 |
D4 |
D5 |
D6 |
L |
L1 |
L2 |
L7 |
L8 |
L9 |
L10 |
M |
CIE-0801R |
8 |
1 |
A |
0.8 |
14 |
21 |
3.4 |
27 |
|
|
16 |
4 |
18 |
10 |
2 |
|
CIE-0802R |
8 |
2 |
A |
1.2 |
14 |
21 |
3.4 |
27 |
|
|
16 |
4 |
18 |
10 |
2 |
|
CIE-1002R |
10 |
2 |
A |
1.2 |
18 |
27 |
4.5 |
35 |
|
|
28 |
5 |
22 |
10 |
2.5 |
|
CIE-1004R |
10 |
4 |
A |
2 |
26 |
36 |
4.5 |
46 |
|
|
34 |
10 |
28 |
10 |
5 |
|
CIE-1204R |
12 |
4 |
A |
2.5 |
24 |
32 |
3.5 |
40 |
|
|
28 |
6 |
25 |
10 |
3 |
|
CIE-1402R |
14 |
2 |
A |
1.2 |
21 |
31 |
5.5 |
40 |
|
|
23 |
6 |
26 |
10 |
3 |
|
CIE-1604R |
16 |
4 |
A |
2.381 |
28 |
38 |
5.5 |
48 |
72 |
10 |
38 |
10 |
40 |
10 |
5 |
M6 |
CIE-1605R |
16 |
5 |
A |
3.175 |
28 |
38 |
5.5 |
48 |
82 |
10 |
42 |
10 |
40 |
10 |
5 |
M6 |
CIE-1605L |
16 |
5 |
A |
3.175 |
28 |
38 |
5.5 |
48 |
100 |
\ |
50 |
10 |
40 |
10 |
5 |
M6 |
CIE-1610R |
16 |
10 |
A |
3.175 |
28 |
38 |
5.5 |
48 |
118 |
\ |
57 |
10 |
40 |
10 |
5 |
M6 |
CIE-1616L |
16 |
16 |
A |
2.778 |
32 |
42 |
4.5 |
53 |
\ |
\ |
38 |
10 |
34 |
10 |
5 |
M6 |
CIE-2004R |
20 |
4 |
A |
2.381 |
36 |
47 |
6.6 |
58 |
72 |
10 |
38 |
10 |
44 |
10 |
55 |
M6 |
CIE-2005R |
20 |
5 |
A |
3.175 |
36 |
47 |
6.6 |
58 |
82 |
10 |
42 |
10 |
44 |
10 |
5 |
M6 |
CIE-2005L |
20 |
5 |
A |
3.175 |
36 |
47 |
6.6 |
58 |
101 |
\ |
51 |
10 |
44 |
10 |
5 |
M6 |
CIE-2020R |
20 |
20 |
A |
3.175 |
39 |
50 |
5.5 |
62 |
\ |
\ |
47 |
10 |
41 |
10 |
5 |
M6 |
CIE-2505R |
25 |
5 |
A |
3.175 |
40 |
51 |
6.6 |
62 |
82 |
10 |
42 |
10 |
48 |
10 |
5 |
M6 |
CIE-2505L |
25 |
5 |
A |
3.175 |
40 |
51 |
6.6 |
62 |
101 |
\ |
51 |
10 |
48 |
10 |
5 |
M6 |
CIE-2510R |
25 |
10 |
A |
4.763 |
40 |
51 |
6.6 |
62 |
|
10 |
75 |
10.5 |
48 |
10 |
5 |
M6 |
CIE-2525R |
25 |
25 |
A |
3.969 |
47 |
60 |
6.6 |
74 |
\ |
\ |
57 |
12 |
49 |
10 |
6 |
M6 |
CIE-3205R |
32 |
5 |
A |
3.175 |
50 |
65 |
9 |
80 |
111 |
10 |
55 |
12 |
62 |
10 |
6 |
M6 |
CIE-3205L |
32 |
5 |
A |
3.175 |
50 |
65 |
9 |
80 |
102 |
\ |
52 |
12 |
62 |
10 |
6 |
M6 |
CIE-3210R |
32 |
10 |
A |
6.35 |
53 |
65 |
9 |
80 |
135 |
16 |
69 |
12 |
62 |
10 |
6 |
M8*1 |
CIE-3210L |
32 |
10 |
A |
6.35 |
50 |
65 |
9 |
80 |
162 |
\ |
90 |
12 |
62 |
10 |
6 |
M6 |
CIE-4005R |
40 |
5 |
B |
3.175 |
63 |
78 |
9 |
93 |
108 |
10 |
57 |
14 |
70 |
10 |
7 |
M6 |
CIE-4010R |
40 |
10 |
B |
6.35 |
63 |
78 |
9 |
93 |
137 |
16 |
71 |
14 |
70 |
10 |
7 |
M8*1 |
CIE-4010L |
40 |
10 |
B |
6.35 |
63 |
78 |
9 |
93 |
165 |
\ |
93 |
14 |
70 |
10 |
7 |
M8 |
CIE-5010R |
50 |
10 |
B |
6.35 |
75 |
93 |
11 |
110 |
171 |
\ |
93 |
16 |
85 |
10 |
8 |
M8 |
CIE-5020R |
50 |
20 |
B |
7.144 |
75 |
93 |
11 |
110 |
280 |
\ |
138 |
16 |
85 |
10 |
8 |
M8 |
CIE-5050R |
50 |
50 |
B |
7.938 |
90 |
112 |
14 |
135 |
|
\ |
107 |
20 |
92 |
10 |
10 |
M6 |
CIE6310R |
63 |
10 |
B |
6.35 |
90 |
108 |
11 |
125 |
182 |
\ |
98 |
18 |
95 |
10 |
9 |
M8 |
6310(Germany)R |
63 |
10 |
B |
6.35 |
90 |
108 |
11 |
125 |
182 |
\ |
98 |
18 |
95 |
10 |
9 |
M8 |
CIE-6320R |
63 |
20 |
B |
9.525 |
90 |
115 |
13.5 |
135 |
290 |
\ |
149 |
20 |
100 |
10 |
10 |
M8 |
8010R |
80 |
10 |
B |
6.35 |
105 |
125 |
13.5 |
145 |
182 |
\ |
98 |
20 |
110 |
10 |
10 |
M8 |
8010(P5 GERMANY)R |
80 |
10 |
B |
6.35 |
105 |
125 |
13.5 |
145 |
182 |
\ |
98 |
20 |
110 |
10 |
10 |
M8 |
8020R |
80 |
20 |
B |
9.525 |
125 |
145 |
13.5 |
165 |
295 |
\ |
154 |
25 |
130 |
10 |
12.5 |
M8 |
Model |
Ring number of ball bearing |
Dynamic rated load CaKN |
Static rated load CaKN |
Rigidity KN/μm |
F |
FM |
CIE-0801R |
4 |
105.7 |
216 |
10.7 |
|
CIE-0802R |
3 |
142.2 |
238.8 |
8.2 |
|
CIE-1002R |
3 |
157.6 |
301.7 |
10.1 |
|
CIE-1004R |
3 |
301.8 |
453.9 |
10.4 |
|
CIE-1204R |
3 |
451 |
709.3 |
12.5 |
|
CIE-1402R |
4 |
235.2 |
569.8 |
18.6 |
|
CIE-1604R |
3 |
4.35 |
9.2 |
210 |
420 |
CIE-1605R |
3 |
7.65 |
13.2 |
230 |
460 |
CIE-1605L |
4 |
888.1 |
1525.4 |
22.1 |
43.1 |
CIE-1610R |
3 |
716.4 |
1232 |
16.6 |
32.3 |
CIE-1616L |
1.7*2 |
683.3 |
1298 |
18.6 |
\ |
CIE-2004R |
3 |
5.3 |
12 |
220 |
440 |
CIE-2005R |
3 |
8.6 |
17.1 |
240 |
480 |
CIE-2005L |
4 |
999.3 |
1994.7 |
27.3 |
53.2 |
CIE-2020R |
1.7*2 |
891.1 |
1795.2 |
23.2 |
\ |
CIE-2505R |
3 |
1119.4 |
2581.4 |
33.8 |
65.8 |
CIE-2505L |
4 |
1119.4 |
2581.4 |
33.8 |
65.8 |
CIE-2510R |
3 |
1903.3 |
3695.3 |
34.5 |
|
CIE-2525R |
1.7*2 |
1331.8 |
2805.4 |
29 |
\ |
CIE-3205R |
5 |
1264.1 |
3402.8 |
42.8 |
83.5 |
CIE-3205L |
4 |
1264.1 |
3402.8 |
42.8 |
83.5 |
CIE-3210R |
3 |
3092.6 |
6101.6 |
44.2 |
86.2 |
CIE-3210L |
4 |
3092.6 |
6101.6 |
44.2 |
86.2 |
CIE-4005R |
5 |
1407.1 |
4341.5 |
53.2 |
103.7 |
CIE-4010R |
3 |
3480 |
7979 |
54.6 |
106.4 |
CIE-4010L |
4 |
3480 |
7979 |
54.6 |
106.4 |
CIE-5010R |
4 |
3898 |
10325.7 |
67.5 |
131.6 |
CIE-5020R |
4 |
4621.1 |
11881.3 |
67.9 |
132.3 |
CIE-5050R |
1.7*2 |
4637.6 |
11221.9 |
58 |
\ |
CIE6310R |
4 |
4401.9 |
13611.2 |
84.3 |
164.5 |
6310(Germany)R |
4 |
4401.9 |
13611.2 |
84.3 |
164.5 |
CIE-6320R |
4 |
7401.1 |
19008.8 |
85.7 |
167.2 |
8010R |
4 |
4900 |
17366 |
106 |
207.4 |
8010(P5 GERMANY)R |
4 |
4900 |
17366 |
106 |
207.4 |
8020R |
4 |
8403.2 |
25345.1 |
108 |
210.1 |
1)Ball screw assembly is a high-precise mechanical drive part made up of screw, nut, ball bearing, sealing washer and other components, for there are ball bearing rolling between the screw and nut, the ball screw can receive high movement efficiency, compared with slide guide screw, the drive torque is under 1/3. So that it is easy to translate turning movement to straight-line movement, also, it is easy to translate straight-line movement to turning movement. It is a kind of further expansion and development of traditional slide guide screw. The profound significance of this development is the same as the transformation brought by rolling bearing to slide bearing. Due to its fine friction character, ball screw assembly is widely used in various industrial equipments, precise apparatus and precise numerically-controlled machine tool. Especially in recent years, work as executive unit of straight-line drive of numerically-controlled machine tool, it is broadly used in machine tool industry, and greatly promotes the numerically-controlled development of machine tool industry. All of these lie on several fine characters as follows:
High drive efficiency, high orientation precision, reversibility of drive, long service life, good synchronous performance
Because the ball screw assembly has smooth operation, eliminates axial clearance, with consistency of production, when it adopts several sets of ball screw assembly projects to drive a same device or several same parts, it can receive excellent synchronous working.
|
2)It not only can feed slightly, but also can feed at high speed. Because of ball bearing’s rolling, ball screw has tiny starting torque, will not cause crawl or creepage phenomena, which are easy to come forth in slide movement, so that it can guarantee to realize precise micro feeding. On the other hand, with high efficiency, small friction and low heat, the ball screw assembly can carry out high-speed feeding at the same time. |
3)Without clearance and with high rigidity. Adopt Gothic groove shape (refer to following picture), the axial clearance is regulated to infinitesimal and can not turn randomly. Besides, as the ball screw assembly can be added pressure in advance, the axial clearance can achieve zero or below zero even more after adding, thus high rigidity is received.
Gothic groove |
4)Adopt inner circulation mode to work (refer to following picture)
This method is to make steel balls roll along the groove of inner circulator, get across the tooth peak of screw sidelong and return to origin. Generally speaking, a circle of steel ball implements a circulation. One end of the screw should be at least if using this circulation method, used in small screw diameter, adopt metal circulator. |
5)Material and heat treatment
|
Material |
Heat treatment |
Rigidity |
Screw |
S55C |
High-frequency quench |
HRC56~62 |
Screw cap |
SCM420 |
Cementite quench |
HRC56~62 |
Steel ball |
SCM420 |
Heat treatment |
HRC60 more than |
|
Precision of ball screw assembly |
Feature of ball screw |
Precision of ball screw assembly |
Selection step of ball screw |
Safety use of ball screw assembly |
1. Lead precision. Lead precision of ball screw of DAVID Mechanical and Electrical Making Co., Ltd. takes ISO 3408-4 as base, and according to using range and requirements, it is divided into orientation ball screw assembly (P) and transmission ball screw assembly (T), and the precision is divided into seven grades, they are 1,2,3,4,5,7 and 10, grade 1 is the highest.
2. Change volumes within random 300mm journey and 2 π radian journey are as follows:
Symbol |
Inspection content |
Symbol |
Precision grade |
1 |
2 |
3 |
4 |
5 |
7 |
10 |
1 |
Change volume within random 300mm journey |
V300p |
6 |
8 |
12 |
16 |
23 |
52 |
210 |
2 |
Change volume within random 2π radian journey (this item is only suitable for P type ball screw assembly) |
V2πp |
4 |
5 |
6 |
7 |
8 |
|
|
1. Clearance at axial direction. Preloading grade of axial clearance of COMTOP precise ball screw is as follows:
Grade |
P0 |
P1 |
P2 |
P3 |
P4 |
Clearance |
With |
Without |
Without |
Without |
Without |
Pre-pressure |
Without |
Without |
Light |
Middle |
Heavy |
1. Reference values of selected precision, clearance, preloading grade and screw cap
Precision |
Preloading and clearance |
Screw cap |
Screw |
C10 |
(P0) with clearance |
Single screw cap |
Rolled Steel Grade |
C7 |
P1 or P0 (Standard) |
According to COMTOP catalog |
Rolled steel or Ground Grind |
C5 |
P1 or P2 (Standard) |
According to COMTOP catalog |
Ground Grind |
C3 |
P1 or P2 (Standard) or P3 |
According to COMTOP catalog |
Ground Grind |
1. Clearance (P0)
Rolled steel or Ground Grind ball screw (P0) max axial clearance Unit: mm
Dimension of outer diameter of screw |
Max axial clearance of Rolled Steel ball screw |
Max axial clearance of Ground Grind ball screw |
Miniature ball screw with diameter of 04-14 |
0.05 |
0.015 |
Middle dimension of ball screw with diameter of 15-40 |
0.08 |
0.025 |
Large dimension of ball screw with diameter of 50-100 |
0.12 |
0.05 |
1.
Reference value of preloading (P2) in common use
Specification |
Spring force of single screw cap (KG) |
Spring force of double screw cap (KG) |
1605 |
0.1-0.3 |
0.3-0.6 |
2005 |
0.1-0.3 |
0.3-0.6 |
2505 |
0.2-0.5 |
0.3-0.6 |
3205 |
0.2-0.5 |
0.5-0.8 |
4005 |
0.2-0.5 |
0.5-0.8 |
2510 |
0.2-0.5 |
0.5-0.8 |
3210 |
0.3-0.6 |
0.5-0.8 |
1040 |
0.3-0.6 |
0.5-0.8 |
5010 |
0.3-0.6 |
0.8-1.2 |
6310 |
0.6-1.0 |
0.8-1.2 |
1. Precision of axis
Model\ Grade of outer diameter of guide screw |
C7 |
C10 |
1605 1610 2005 2505 |
0.04mm |
0.10mm |
2510 3205 3210 |
0.07mm |
0.17 |
4005 4010 5010 |
0.10 |
0.20 |
- Precision and testing method of precision of ball screw’s installation position:
- Take axes A of Thread Groove as frame of reference to test run-out value of circumference at radial direction.
- Take axes F, which lies in the supporting part of screw, as frame of reference to measure coaxial degree of accessories’ installation position.
- Take axes E, which lies in the supporting part of screw shaft, as frame of reference to measure right angle degree of the surface of supporting part.
- Take axes G of screw as frame of reference to measure right angle degree of screw cap’s datum plane or the installation surface of flange.
- Take axes A of screw as frame of reference to measure coaxial degree of circle (cylinder type) of screw cap’s peripheral.
- Take axes C of screw as frame of reference to measure parallelism of peripheral of screw cap (flat type installation surface)
- General run-out valve of screw axes at radial direction.
- The precisions here take JIS B 1191、1192 as standard.
- B: Testing method of precision of installation position:
Put the ball screw on V-shaped cushion iron of AA at the time of testing, meanwhile, let testing head of the two dial indicators vertically touch surface of axial column respectively, slowly turn guide screw and write down change range of reading of the two dial indicators, calculate max tolerance of the reading, that is required warp, then check the guide screw with checkout apparatus, control this warp within allowed range through the control to guide screw.
Note: allowed error
- When l6>l, the allowed error is t7a<=t7p(l7/l)
When testing, put the ball screw in V-shaped cushion iron terrine of AA, let the gauge head vertically touch column surface of guide screw at the distance of 15, turn guide screw slowly, write down max tolerance value of the reading, test within fixed measuring interval over and over again to receive max value.
Note: when l1<2l5, can be measure at l1/2.
|
auto bearing & ball bearing
|
 |